FINISHING MATERIALS FOR FACADES.
- Rustam Malikov
- Sep 12, 2023
- 15 min read
Updated: Sep 15, 2023
The homeowner often contemplates how to dress the exterior of their house beautifully and practically, which facade materials to choose for finishing, and how to select and calculate them correctly. The facade is the face of the building, and besides its aesthetic function, it protects the building from various natural influences.
We recommend moving away from dull, monochromatic facades, where only one type of finish is applied to the exterior walls. The trend of the last decade is a combined facade, for example, a combination of wood and clinker tiles, ceramic granite, and stucco. Such a type of finishing will always look expensive and interesting.
What types of finishing materials are available for facades:
1.Ceramic granite

Modern porcelain tiles for cladding building facades
Ceramic granite is an exceptionally durable, high-tech, and environmentally friendly cladding material of the extra-class. It is produced from the purest natural raw materials, various mixtures of crushed minerals (quartz, feldspar) based on high-quality kaolin clays, spars, and feldspars by pressing at high pressure and subsequent firing at very high temperatures (over 1200 degrees Celsius).
Ceramic granite is widely used not only as a cladding material for building facades but also in the interiors of private apartments, houses, and public spaces.
The installation of ceramic granite on facades can be done in two ways:
Using a complex framework system of guiding profiles to which the cladding is attached - following the technology of ventilated curtain walls.
Using construction adhesive compounds.
Typically, building facades are clad with ceramic granite in the following formats: 300x600, 600x600, 600x1200, 400x800, 800x2400, 1200x1800 mm with a thickness of 8-20 mm.
Advantages of the material:
Advantages of the material:
Low moisture absorption due to the fact that ceramic granite is a low-porosity material.
Resistance to external chemical exposure and wear. The highest level of resistance to the wear of aggressive substances.
High operational properties make it possible to use it for finishing public buildings (both exterior and interior) with high foot traffic, such as airports, train stations, shopping centers.
Mechanical strength and load resistance. Impact resistance against high pressure on the surface of ceramic granite allows for its use as flooring in industrial facilities.
Frost resistance and temperature stability. Even sharp temperature fluctuations within 100 degrees Celsius do not affect the properties of ceramic granite.
Scratch resistance.
Stain resistance.
Variety of surface types and color options.
Disadvantages of the material:
Structure. Installation of ceramic granite on projects is impossible without a special tile cutter (due to the high density of the material).
Cost. The high price fully corresponds to the declared quality, service life, and reliability.
Slippery surface.
2. Facing brick (clinker tile, clinker)
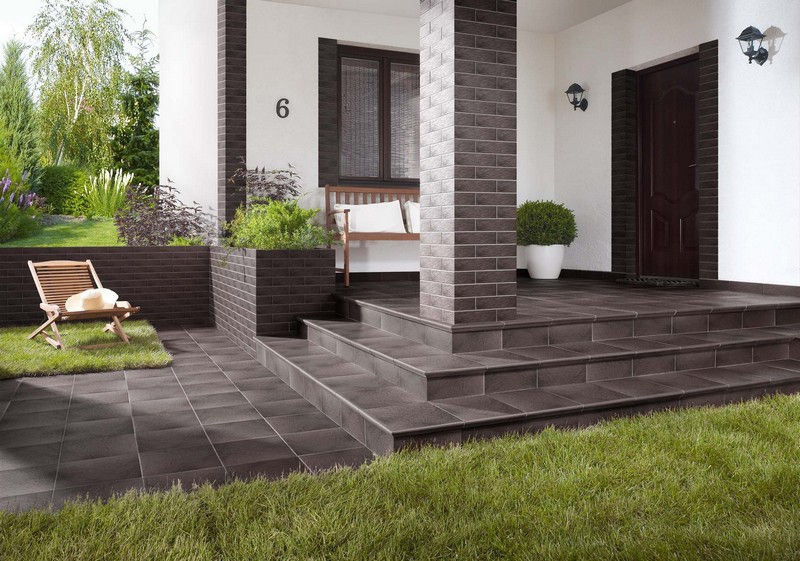
Modern clinker tile
Clinker tile, as a type of ceramic facade tile, is a product known for its high strength and low water absorption, serving as a decorative material that does not pose problems in the subsequent maintenance of building facades. This material combines centuries-old traditions of tile craftsmanship with modern possibilities and technological diversity.
Clinker, like traditional ceramics, is produced by firing clay. To make this material, refractory kaolin clays with different sintering intervals are used. The clay is fired at very high temperatures of 1200-1300°C.
Facade clinker is available in various forms in the finishing materials market: as bricks, tiles, or thermal panels. Due to the wide variety of this material and the large number of manufacturers, the sizes of clinker tiles vary significantly. For example, the format of one clinker brick can be 240x71x5 mm, while a clinker brick of a stretcher (elongated) shape can measure 590x52x12 mm. (Clinker bricks have corner (additional) elements, which should also be taken into account when purchasing the material). For comparison, the size of thermal panels is 1028x616x65 mm, and clinker tiles are 9-14x240x71 mm.
Advantages of the material:
High strength and durability. Walls made of clinker bricks remain in pristine condition for many years.
Low water absorption. Even prolonged contact with water will not harm clinker.
Frost resistance - up to 200 cycles. Ability to withstand numerous freezing-thawing temperature cycles.
Resistance to chemical exposure. Clinker is not affected by salts, acids, alkalis, or ultraviolet rays.
Environmental friendliness. An entirely harmless building material made entirely from fired clay.
Variety of surface types and color options.
Disadvantages of the material:
High cost.
The use of a special mortar. Different types of clinker (clinker brick, hand-molded clinker, etc.) require their own special adhesive mortar based on trass (finely crushed volcanic stone)
3. Natural wood
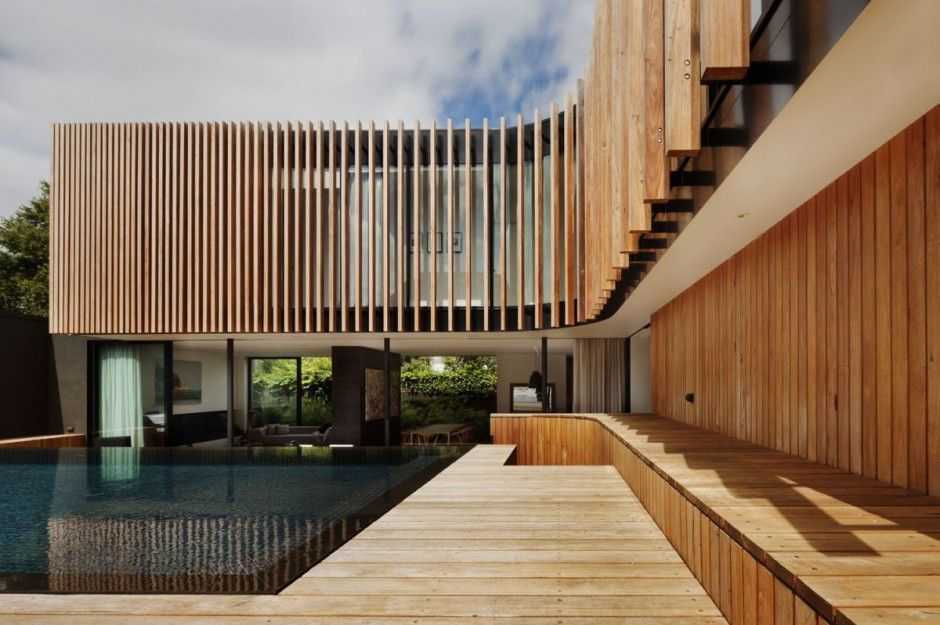
Exterior finish of the house with natural wood
Wood is widely used in various areas of human activity. For many centuries, it has been considered the best building and finishing material for various purposes. Architects favor natural wood because structures made from it are eco-friendly, lightweight, and require less energy. Designers love to use wooden products extensively in interior finishing. Therefore, natural wood for facade cladding is the best choice for those who appreciate the natural beauty of organic shapes, tones, and textures.
Facade cladding made from natural wood can be combined with other materials, such as stone, wrought iron, vinyl siding, etc.
In exterior house cladding, coniferous and deciduous wood species are successfully used: pine, spruce, larch, oak, cedar, ash, beech - these are the most cost-effective wood species. Exotic tree species (cumaru, ipe, zebrawood, teak, etc.) are also available in the materials market, but their practicality and compatibility with Russian climate conditions are questionable.
Although for building facades, it is advisable to use thermally treated wood as it is more practical in use.
Typical size range: wooden board - width 10-250 mm, length 2-6 m, thickness 10-40 mm, shingle - length 20-80 cm, width 60-250 mm, thickness 6-15 mm.
The finishing materials market offers wooden facade boards in the form of:
Planks - boards with chamfers removed from all four corners.
Lining - thin lining boards with a tongue and groove joint.
Imitation of timber (false timber) - boards that closely mimic the walls of a log house.
Blockhouse - semi-round boards that precisely imitate the walls of a log cabin.
Clapboard (shingle, shakes) - small-sized planks made by hand or by mechanized methods.
Battens - flat wooden boards.
The installation of all wooden facades is carried out on a wooden or metal framework following the principle of ventilated facades.
Among the unquestionable advantages of cladding the facade with natural wood, it is worth noting the wood's ability to resist significant mechanical loads, resistance to oxidation, and resistance to the action of aqueous solutions of salts and acids. Some wood species have unique resistance even to moisture.
Advantages of the material:
High aesthetic qualities.
Exceptional insulating properties in terms of heat, sound, and electricity.
Protective properties.
Environmental friendliness.
Disadvantages of the material:
Not as long-lasting as natural stone or facing brick.
Requires additional financial costs for maintenance to extend its service life (periodic painting, treatment with antiseptics, and other protective compounds).
Combustible material, not fire-resistant.
4. Artificial stone

Artificial stone finishing
Modern artificial stone is a material that allows for the imitation of the cut of natural stone when laying. It can resemble fragments of natural stone, gravel, boulders, cobblestones, or, conversely, sawn stone of regular shape; it can also be presented in the form of bricks.
Artificial stone for facade finishing can be divided into two types of products:
Various types of synthetic stone products based on a polyester layer and filler made from crushed natural stone.
Facing products made from colored concrete with a relief surface and a color close to natural stone.
Artificial stone made from colored concrete is used for both decorating and cladding the surfaces of buildings and structures and for interior decoration. Artificial stone is very convenient for installation compared to natural stone because it is technically pre-cut tiles with one flat side.
Such stone can be made from white or gray cement, artificial or natural sand, a filler that surrounds the mass of the stone (expanded clay, expanded perlite, ceramic crumb, or natural pumice), fragments of natural stone, and regular water.
When choosing artificial stone, it is recommended to inquire with the supplier about where the stone was manufactured, as Russian-made products are better adapted to our climatic conditions.
Advantages of the material:
Low cost.
Easy installation.
Minimal load on the facade.
Lightweight product.
Variety of textures and color options.
Disadvantages of the material:
Shorter service life (compared to natural stone).
Susceptible to physical wear and tear, quick abrasion.
Fragility. Under strong mechanical stress, the material can crumble because it is not a solid product.
Limited use. Artificial stone is not suitable for creating ventilated building facades.
Not frost-resistant, unable to withstand rapid temperature fluctuations. Microcracks can even appear on the artificial surface in severe frost
5. Natural stone

Exterior façade finishing with natural stone
Cladding facades with natural stone is a finish for the ages. Natural stone, as they say, 'neither burns nor drowns.' And it truly does not burn, rust, rot, age, or deteriorate at all. It is truly an eternal material. There are over 8,000 types of stones, but not all of them are in demand or sought after. Marble, granite, labradorite, slate, sandstone, and limestone are indispensable in construction. To choose the right type of natural stone for specific tasks, one must know the material's physical and mechanical properties. For example, when cladding a building, it is necessary to consider the stone's high resistance to low temperatures and frost resistance. For cladding stairs, one must select a stone resistant to wear, mechanical impacts, and shocks.
The most common types of natural stone used in exterior facade finishing include:
Wild natural (unprocessed) stone.
Dagestan stone.
Sandstone.
Limestone.
Dolomite.
Travertine.
Marble.
Granite.
Bouldery stone.
During quarrying and processing, stones undergo mechanical treatment, cutting, grinding, milling, and are brought to the market in various forms, including:
Raw: This type of stone is practically untreated, preserving its natural appearance.
Bush-hammered: The surface features point-like indentations created by impacts. The surface is treated using a grinder and special attachments.
Honed: This type has a smoother texture, but traces of mechanical treatment are intentionally preserved.
Sawed: The stone retains its natural roughness. Flame treatment is often used during processing.
Brushed: A matte surface created with fine abrasives.
Polished: The stone is processed until it has a mirror-like shine.
Natural stone for facade cladding is cut into various-sized tiles, such as 50x160 mm, 80x160 mm, 300x600 mm, 350x750 mm, with a thickness of 20-30 mm. However, every supplier aims to meet the customer's needs and offers large-format slabs or tiles tailored to your specifications, depending on the goals and capabilities of the consumer.
Advantages of the material:
Wide range of applications.
Unique material texture.
Highest protective abilities.
Thermal regulation, maintaining an optimal microclimate. In summer, stone cladding will keep the house cool, while in winter, it will provide warmth.
Longevity and strength. Stone is not susceptible to natural deterioration.
Frost resistance. Resistant to abrupt temperature changes.
Vapor permeability, the ability to 'breathe.'
Environmental friendliness.
Disadvantages of the material:
Significant weight of products.
High cost.
Installation. Working with stone requires a certain level of experience, skill, and qualified installers.
6. Facing brick

Building finishing with facing brick
Facade brick is designed for the external finishing of walls and building foundations, typically serving both a structural and decorative role. It can effectively protect the exterior walls of a building and enhance their load-bearing capacity.
To improve its decorative properties, various additives such as pigments and mineral aggregates are incorporated into the brick's composition, and it undergoes special treatments like engobing and glazing.
Applications of facade brick include construction (for building structures and fencing), restoration work, facade cladding, interior decoration, and more. Different shapes and colors of bricks allow for recreating fragments of historic buildings and emulating various architectural styles.
Types of facade bricks include ceramic, clinker, silicate, and hyper-pressed. Facade bricks come in various sizes, not limited to standard rectangular forms, including DF, 2DF, WDF, WF, MRT P/MRT N/MRT R, FAT N/FAT R, NRT Hollka, VAT R/VAT N with 5 or 6 angles or with rounded edges.
Common dimensions of standard rectangular bricks: width 100-120 mm, height 50-110 mm, length 190-250 mm.
Advantages of the material:
Long service life.
High reliability and mechanical strength.
Good thermal insulation properties.
Precise geometric parameters with very smooth edge lines.
Resistance to abrupt temperature changes.
Low maintenance requirements. It absorbs dirt and grease well.
Eco-friendliness.
Disadvantages of the material:
Formation of white efflorescence (salt deposits), which can affect the appearance of the building.
Relatively expensive as an external finishing material.
7. Facade plaster finishes

Combined facade finishing - decorative plaster and artificial stone
Stucco is a construction material consisting of sand and cement with added solid inclusions. It is used for leveling surfaces, adding texture and shape, and serves decorative, sanitary-technical, and protective-construction functions.
Based on its composition, stucco can be categorized as follows:
Mineral (based on cement).
Silicone (based on various synthetic resins such as silicone).
Acrylic (based on acrylic resin with pigment additives).
Silicate (based on "liquid glass," a mixture of potassium carbonate on an alkaline basis, natural quartz sand, potassium derivatives, and various pigmentation granulates).
Regardless of their composition, cost, and the finish obtained, all stucco types can be divided into dry mixes that require dilution before application and ready-to-use suspensions.
Significant advantages of stucco include the quality of its composition, its elasticity, and its high adhesion to various surfaces. Such a composition is resistant to various mechanical and atmospheric influences. The finishing layer will not be damaged by moisture, and the material does not emit toxic substances. Stucco can be applied for a relatively long time without losing its properties. The market offers a wide range of textures and color options for both exterior and interior work.
As a drawback of this finishing material, it can be noted that due to its lack of electrostatic properties, stucco may become dirty. However, thanks to its low dirt absorption, dirt will not penetrate the coating's structure, and it can be easily cleaned.
Let's take a look at some popular types of exterior stucco finishes that are in high demand among consumers.
Below, we will consider some popular types of facade plaster that are in high demand among consumers:
7.1. Bark beetle

The facade finishing of 'Koroe House
Koroyed is the most popular facade stucco among all the options available. It contains mineral or marble chips. Unlike regular stucco, Koroyed has small granules or particles that, when applied, leave an unusual trace on the wet stucco, resembling the paths left by the pest known as "Koroyed." Depending on the application method, these "paths" can take various shapes.
Typically, "Koroyed" stucco is used as a decorative finishing material for exterior walls. It is used to a lesser extent for interior walls and even less frequently for ceilings.
Advantages of the material:
Frost resistance and resistance to abrupt temperature fluctuations.
Resistance to atmospheric precipitation and ultraviolet rays, preventing fading from sunlight.
Fire resistance.
Resistance to natural and mechanical damage, such as water flow, hail impacts, light tapping, and more.
Additional wall sound insulation.
Disadvantages of the material:
In case of improper application and the formation of chips, it may not be possible to patch them with a uniformly colored composition.
Strict adherence to application recommendations is required (specific outdoor air temperature, humidity conditions, surface cleaning from previous layers)
7.2. Venetian plaster

Decorative "Venetian" plaster in facade finishing
Venetian plaster is no less popular as a facade finish. The durability of the resulting coating is at a high level. Without any significant changes, the coating can last for over a decade.
The composition of this plaster includes natural components such as gypsum, marble, and lime, making it environmentally friendly and classified as a mineral plaster. The material is quite flexible due to the use of polymers, which means the coating will not crack.
Advantages of the material:
Versatility: It can be applied to various substrates such as concrete, aerated concrete, brick, wood, and more.
Absence of seams and joints.
Impact resistance and longevity.
Resistance to ultraviolet rays and natural weathering.
Disadvantages of the material:
Expensive finishing option.
Requires skilled craftsmen for application.
Adherence to strict application recommendations.
7.3. Textured plaster (plaster for brickwork)

Plastering under brick
Textured plaster, often used as a finish under brick walls, is a versatile and visually appealing choice for interior and exterior surfaces. Here's everything you need to know about textured plaster:
Definition: Textured plaster, also known as textured finish or textured coating, is a specialized type of plaster applied to surfaces, including walls and ceilings, to create a unique texture or pattern.
Purpose: Textured plaster serves both functional and aesthetic purposes. It enhances the appearance of a wall or ceiling, adds depth, and can help conceal imperfections in the substrate. Additionally, it can provide some insulation and soundproofing properties, depending on the thickness and composition.
Application: Textured plaster is typically applied by skilled craftsmen or plasterers who use various techniques to achieve different textures. Common application methods include troweling, spraying, or even rolling the plaster onto the surface.
Types of Textures: There are numerous texture options available, each creating a distinct visual effect. Some popular textured finishes include:
Rustic Brick: This texture mimics the appearance of aged or weathered brickwork, making it a great choice for creating a rustic or vintage ambiance.
Knockdown: In this finish, the plaster is initially applied with a trowel and then partially flattened or "knocked down" to create a textured, but not too rough, surface.
Skip Trowel: Skip trowel texturing involves applying plaster unevenly with a trowel, resulting in a random, mottled appearance.
Swirl: Swirl patterns are created by swirling the plaster with a tool or trowel, producing elegant, flowing patterns.
Stucco: Stucco is a well-known textured plaster finish, often used on exteriors. It provides a rough, uneven texture that adds character and durability to walls. In summary, textured plaster is a versatile and aesthetically pleasing choice for adding character and visual interest to walls and ceilings. With various texture options available, it can be tailored to suit a wide range of design preferences and architectural styles, making it a popular choice among homeowners and designers alike.
Advantages of the material:
Strength, durability, practicality.
Concealment. Plaster can be used to camouflage irregularities and cracks.
Resistance to external factors.
Versatility.
Disadvantages of the material:
Relatively high cost.
Complexity of removal.
Requirement for surface cleanliness.
8. Exterior wallpaper

Exterior wall coverings
Exterior wallpaper has emerged relatively recently in the market of exterior finishing materials but has already gained significant popularity. It is presented in the form of roll (less commonly liquid) covering material used for cladding facades. It consists of adhesive made of acrylic resin and binding additives, as well as reinforcing profiles with a fiberglass mesh for strengthening the joints between rolls on the facade.
Exterior wallpapers can be:
Non-woven wallpapers, based on compressed cellulose molecules, covered with foamed vinyl. They come in smooth and textured variants.
Mineral-based wallpapers, made from glass fiber (a mixture of limestone or dolomite fibers with inclusions of quartz sand). Various volumetric patterns are applied to the outer surface.
Flexible stone wallpapers, based on marble, granite, or quartz of various fractions, affixed to a flexible elastic base using transparent polymer acrylic binders. These wallpapers are also called "flexible stone" or "flexible facade tiles." For additional protection, such wallpapers are coated with varnish.
Wallpapers look best on buildings with simple shapes, such as rectangles or squares. An interesting design choice is to use exterior wallpapers on only a portion of the wall rather than covering the entire building.
Advantages of the material:
Protection of the facade from natural elements and mechanical damage.
Waterproof, frost-resistant, capable of withstanding temperature fluctuations.
Long service life, depending on the manufacturer, up to 25-30 years.
Resistant to cracking.
Non-flammable material.
Environmentally friendly.
Disadvantages of the material:
Relatively high cost.
9. Siding

The building is clad with facade siding
Siding is the cladding of building walls with facade elements such as strips (laminates) or pre-made panels made of various materials in different shapes, sizes, and colors. Facade panels are in high demand as they significantly simplify installation and reduce the time required.
One side of the siding has a fastening base with perforations, allowing the panels (or slats) to be secured with screws to the sheathing. This makes them easy to install or replace in case of damage.
Siding serves two important functions:
Utility: It protects building walls from external natural factors, mechanical damage, and chemical exposure.
Aesthetic: It decorates the facade and gives the building an attractive appearance.
The range of siding sizes varies significantly due to the wide variety of materials used for facade finishes. Average dimensions of facade slats or panels are as follows: thickness 0.5-35 mm, width (height) 100-300 mm, length 2-6 m.
Siding comes in several types:
Metal siding, made from metal (steel or aluminum).
DPC siding, composed of processed wood fiber and polymers (polypropylene or polyvinyl chloride).
Fiber cement siding, consisting of cement and reinforcing fiber.
Vinyl siding, based on polyvinyl chloride with various modifiers, colorants, and pigments, as well as other chemical additives.
Acrylic siding, made from acrylic polymers and other chemical additives.
HPL panels, with a core of cellulose impregnated with thermosetting resins and processed under high pressure.
Sandwich panels, consisting of two outer layers of PVC (particleboard, OSB, metal, organite, plastic, or magnesite) with a layer of thermal insulation material (polymer or mineral wool) in between.
Reinforced foam plastic, a sheet of dense foam polystyrene reinforced with a mesh and coated with a special elastic plaster.
Despite the variety of siding materials, they share common advantages and disadvantages.
Advantages of siding materials:
Beautiful, aesthetic appearance for buildings clad with siding.
High durability (up to 50 years).
Low maintenance requirements.
Lightweight and flexible.
High resistance to temperature fluctuations and atmospheric precipitation.
Good protective properties.
Resistance to decay, degradation, and corrosion.
Easy installation.
Disadvantages of siding materials:
Not all types of siding are highly eco-friendly.
Flammability of some siding types and the release of toxic substances in case of fire.
Not all types of siding are sufficiently resistant to mechanical damage.
10. Glass
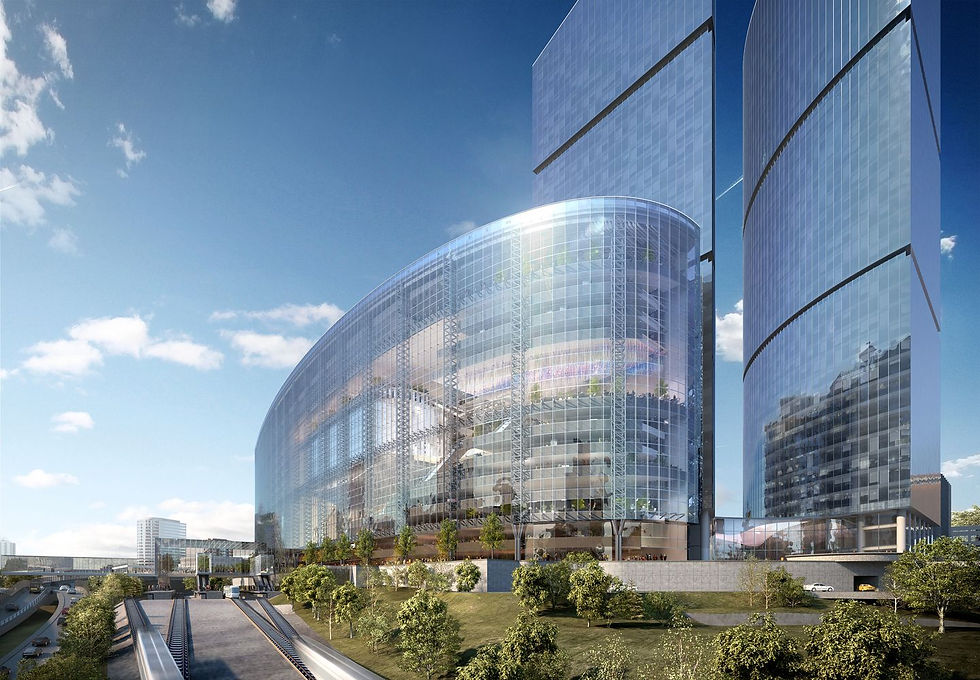
The facades of the building made of glass (SberbankCity office complex in Moscow)
Glass panels give a building an expensive and presentable appearance. They are the perfect solution for multi-story office buildings, shopping centers, public buildings, where significant energy savings can be achieved.
In private construction, transparent cladding is suitable for private residences, country houses, winter gardens, large terraces, indoor pools. Glass panels are made using insulated glass units or polycarbonate. Transparent material with the addition of dyes or one-sided mirror coating is also used in production. Glass is tempered or laminated to make it super strong and impact-resistant.
Glass cladding has excellent sound insulation properties, protects the walls of the house from pollution, and is used instead of thermal insulation systems.
During installation, glass panels are usually attached to the facade using glazing profiles on light-transparent structures. The fastening is done similarly to a ventilated facade.
The following types of glass are used for facade glazing:
Monolithic glass - thick enough, subjected to tempering and thermal strengthening.
Glass laminated with a polymer film - for strength and tinting of transparent glass to the desired color.
Tempered glass - very strong construction made of two or more glasses bonded together with a polymer composition. Such a construction is very difficult to break, and even if the glass is shattered, the structure itself will remain intact.
Insulated glass units - two or three glasses connected by a plastic or aluminum spacer frame. Inert gas is often injected into the insulated glass units, significantly improving their energy-saving characteristics.
The dimensions of glass panels depend significantly on the type of glass chosen for cladding, the facade glazing system, and the specific manufacturer.
Advantages of the material:
High operational qualities and durability.
High strength, resistance to mechanical damage.
Low maintenance requirements.
High thermal and energy efficiency.
Disadvantages of the material:
High cost.
Complexity of design and installation work.
11. Facade metal cassettes (linear panels)

Metal cassettes in building cladding
Facade metal cassettes, also known as linear panels, are special building finishing elements with unique characteristics and a wide range of applications. Here is more detailed information about them:
Purpose and Application: Facade metal cassettes are used to create the external envelope of buildings and structures. They are designed to enhance the building's appearance and protect its walls from external factors. Linear panels are employed in both residential and commercial as well as industrial construction projects.
Materials: Facade metal cassettes can be manufactured from various metals such as steel, aluminum, copper, brass, and others. This allows for material selection based on design requirements, corrosion resistance, and budget considerations.
Design and Finishing: Linear panels offer a wide range of design possibilities. They can be painted in various colors or feature different surface textures and finishes. This makes them an ideal choice for achieving a specific architectural style or building appearance.
Installation and Structure: Facade metal cassettes are mounted onto a suspension system or framework attached to the building's wall. This ensures secure and efficient attachment. The cassettes typically have a locking mechanism for easy and precise interconnection.
Protective and Insulating Properties: Linear panels can possess protective and insulating properties. They can be installed with insulation or soundproofing materials to enhance thermal and acoustic insulation of the building.
Advantages:
Improved aesthetic appeal and design flexibility.
High resistance to mechanical damage and harsh environmental conditions.
Easy installation and maintenance.
Ability to create unique and customized design solutions.
Disadvantages:
Limited sound insulation properties, requiring the installation of insulation materials.
Potential for static electricity accumulation due to the metallic material, necessitating precautions in the design.
Facade metal cassettes (linear panels) are a significant element of modern architecture, providing both protection and decorative enhancement to buildings while allowing for the creation of unique and attractive facades.
Commentaires